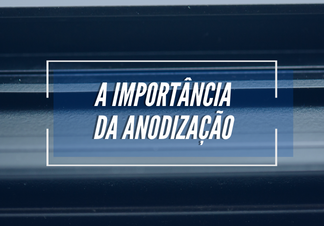
THE IMPORTANCE OF ANODIZING
Much has been said about Anodizing in the machining industry, but how does this process actually contribute to higher quality in industrial components?
Anodizing is an electrochemical forced and controlled oxidation process, applied only to aluminum and its specific alloys. The anodic “layer” (aluminum oxide or alumina) formed presents up to 550 HV10 of hardness and is porous, anhydrous and transparent. It was discovered in laboratory by H. Buff and C.Pollack in 1857, during an experiment about aluminum tending to coat itself with a “layer” (oxide) based on the superficial transformation of aluminum. From this discovery, countless studies were made, but only in 1911 the French Français Saint Martin developed the basic principles for electrolytical oxidation in sulfuric medium.
Although protecting components is the main benefit of Anodizing, the process has several other advantages, especially in the aesthetic aspect of parts, which acquire a matte, colorful and shiny decoration. Additionally, Hard Anodizing (conducted in sulfuric acid and at low temperatures) also presents major gains concerning the quality of components, such as:
- Major resistance to wearing
- High durability
- Electric insulation
- Resistance to corrosion
The Anodizing process has wide and encompassing application, since it can be used in aluminum frames, household items, parts for use in the automotive, aeronautical and defense industries, as well as ornamental architectural elements.
Naturally, aluminum and its alloys suffer the action from oxidizing and abrasive agents when permanently exposed to urban air. Thus, the anodizing treatment is mandatory for extending the work life and quality of components and parts.
In this sense, SAMOT offers Anodizing solutions custom-made for your demand. With a highly qualified team, leading-edge equipment and a complete structure, we are ready to develop projects that increase the durability and resistance of your parts.