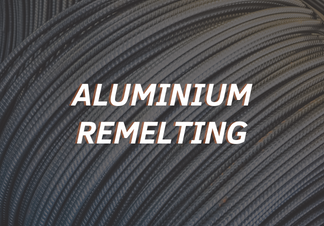
ALUMINUM REMELTING
Aluminum is the most abundant metallic material on the surface of the Earth, and the countries that produce it the most nowadays are large industrial powers: China, Russia, and India. This input is widely used in several industries due to its excellent physical and chemical properties. It is of great commercial importance due to its light weight, electric conductivity, resistance to corrosion and low melting point, which allows its use in different areas.
One of the main advantages of aluminum is its moldability, since it can be extruded in a limitless number of formats for any type of use. It can also be endlessly recycled. The recycling process uses only 5% electricity, and according to data from the International Aluminum Institute (IAI), it releases only 5% of the greenhouse effect gases when compared to the primary production of aluminum (obtained through bauxite, the aluminum ore).
Fun fact: Melting is a term used for any process with liquid metal. Remelting is a term specifically used for semi-continuous melting specific for the manufacturing of billets (which is the process performed in our Altref Unit).
The remelt furnaces are the most widely used in manufacturing billets, both for their cost-benefit and for their greater thermal efficiency and lower oxidation loss.
The control of the primary aluminum raw material or the process return, joined to the temperature control and treatment of the liquid metal guarantee mechanical properties for several extruded product applications, which can have different physical and chemical characteristics to serve a variety of applications.
The alloy chemical elements are added within the minimum and maximum limits to ensure the properties required with the necessary characteristics for the end user. We work with the following alloys: 1050; 2011; 6061; 6063; 6026; 6042; 6082; 6351; 6262; and 7075.
The chemical composition control is made by spectrophotometer, with inspection in the several stages of production, from the receipt of the raw materials through the melting and treatment of liquid metal steps, and in the manufacturing process of each billet.
The liquid aluminum receives grain refiner (TiBAL) to ensure the refined and homogeneous structure. It is also degassed for removing the hydrogen through the Foundry Degassing Unit, and filtered in ceramic filter to retain particulates and oxide films.
We use the Vertical Direct Chill (VDC) Wagstaff system for the manufacturing of the billets, ensuring the controlled metallographic structure for better subsequent processing.
A homogenization thermal treatment is also performed on the billets to release tension and for solid diffusion and control of the alloy element phases with the purpose of having very close metallographic structures through the entire billet, and from billet to billet.
The use of aluminum is also a sustainable option, since the material can be endlessly recycled for other purposes, and its processing demands lower environmental impact than the primary aluminum.
ALTREF, specialized in the production of aluminum, is part of the SAMOT and with all its technical know-how and training, is able to provide all the aforementioned advantages. In addition to the quality and versatility of the special aluminum alloys, it also contributes with lower environmental impacts to provide the best possible products to our clients.