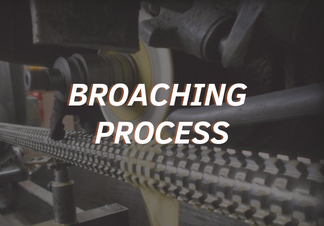
BROACHING PROCESS
Machining is a very popular manufacturing process. However, some parts present profiles with complex geometries, which can render the machining procedure expensive and time consuming. The broaching procedure was developed in order to process these high volume, complex profile parts.
The broaching operation consists in removing surface material from a metallic part in a progressive manner. This process uses a multi-cut tool, with its cutting blades placed in series, which go over the part in a straight displacement, deburring, finishing and calibrating it.
The machine performing this operation is called a broaching machine. It has a straight line movement, which can be either vertical or horizontal, with the option for mechanical and hydraulic commands. Two types of broaching procedures can be performed with the machines: external and internal broaching.
External broaching: The operation is performed on the external surface of the part, providing finishing or semi-finishing to its profiles.
Internal broaching: This operation allows changes to center holes and transform the profile of a part. The purpose may be used to open cavities for woodruff keys in cylindrical holes, or transform cylindrical hole profiles in channeled, grooved, square, hexagonal, and other types of profiles. This operation is made on a hole that was previously open by any other process.
In order to reach all those benefits, the broaching process can be used on the production of large volumes of parts, since each operation requires the designing and fabrication of a unique and complex tool, of high cost.
The broaching process can be widely applied according to the client's needs, and Samot has the technical skills and specific machinery to fully meet such demands, allowing an economical production, with a low cost per machined part.