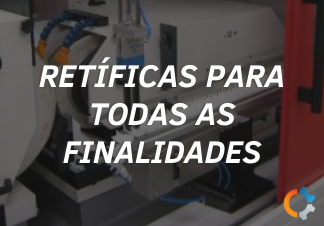
WHAT IS THE IMPORTANCE OF GRINDING?
Grinding is a mechanical machining process in which the removal of the material is established by the contact between the part and an abrasive tool (grindstone), which turns in high rotation while the part has a lower speed. The objective of grinding is to reduce the roughness, protrusions, or recesses of machined surfaces using a machine-tool, such as: drill, lathe, planer, or milling machine, for instance, which ensure the quality and precision of measures. This operation is often used in the mechanical metal industry with finishing purposes.
Origin of Grinding
The first mechanized cylindrical grinding operations were carried out by the North-American company Pratt & Whitney, around 1860 in the United States, where the first grinding machines appeared in the head office of the company Norton Emery Company, by engineer Charles Moseley. However, it was only in 1875 that engineer Joseph Brown, one of the founders of the company Brown & Sharpe, from Providence, Rhode Island, developed a first model of grinding machine intended for sale.
Models of Grinding Machines Utilized at SAMOT
Technology advances are constant, and therefore, the level of quality requirement in the market increased significantly, as a result of the evolution in the design of the products, the parts became even more precise and with strict degree of superficial finishing, being necessary to aggregate grinding machine processes to meet the specifications.
To meet the market requirements, Samot uses different models of grinding machines, which seek to meet the several needs.
Centerless Grinding Machine
The Centerless grinding machine machines parts with outer cylindrical surfaces, such as axles, pins, bushings, rolls, and pipes, among others. Therefore, a centerless grinding machine is used, hence the designation Centerless. In this process, the part is not fixed, but leans against a ruler and is led by the cutting grindstone and the dragging grindstone. They can be divided into 2 types of processes: Centerless Grinding Machine by Passage (the only diameter to be ground) and Centerless Grinding Machine by Immersion (several diameters to be ground at the same time). Typically used for serial production.
Cylindrical Grinding Machine
The cylindrical grinding machine is an important grinding process, responsible for grinding simple or complex cylindrical parts, with or without symmetry, such as axles, stepped axles, rods, cylinders, flanges, pins, conic pins, and many other parts. Its main characteristics include: possibility of obtaining closed dimensional tolerance, compatible geometric tolerance, and low roughness.
Plane Grinding
Plane grinding grinds faces and profiles of parts with several angles, geometries, and channels. Therefore, it is necessary to attach the parts to a magnetic table or a device, leaving one of the faces or profile free to be ground.
Double-Face Grinding
Double-face grinding consists of a service that grinds both faces of a part simultaneously. Due to the simultaneous grinding of two faces and regardless of the type or specification of each part, it ensures perfectly smooth surfaces, without any grinding failures, applying all definitions of roughness and width to the standard needed by the customer, and has become one of the fastest processes in the market.
Blanchard Grinding
Blanchard grinding is a quite robust machine when compared with other models existing in the market, its major differential is the rotating table of the magnetic type, the parts of which do not move, which allows grinding to be made in a more precise manner, thus obtaining attractive cost-efficiency.