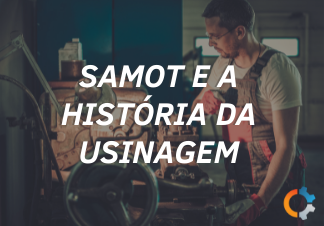
A evolução da usinagem
Os primeiros relatos do processo de usinagem datam o ano de 700 antes de Cristo, em que o homem já buscava moldar materiais brutos, principalmente os feitos de ferro. Porém, foi somente no século XVII que apareceram as primeiras siderúrgicas de aço, começando um processo de revolução e aprofundamento em processos como a usinagem.
Os primeiros tornos de que se tem conhecimento do funcionamento foram chamados de Tornos de Vara, muito utilizados por artesãos durante toda a idade média e meados do século 19. Apesar disso, provas arqueológicas e desenhos egípcios mostram que esta máquina já existia há muitos anos, alguns datados de 300 anos antes de Cristo.
No sistema de vara, a peça a ser trabalhada era amarrada com uma corda presa em uma vara sobre a cabeça do artesão e sua outra extremidade era amarrada a um pedal, que quando pressionado puxava a corda fazendo a peça girar. A vara, por sua vez, fazia o retorno. Por ser fácil de montar, esse tipo de torno permitia que os artesãos se deslocassem facilmente para lugares onde houvesse a matéria prima necessária para o trabalho.
No final do século 15, Leonardo da Vinci (inventor, cientista, pintor, escultor, entre muitas outras funções, nascido na Itália em 1452) desenhou três máquinas em uma página. A primeira delas, um torno, já utilizava uma roda que ainda funcionava somente para a inércia. A segunda era uma serra e a terceira, um sistema que usava um pedal para girar uma roda, que poderia ser anexado a diversos dispositivos. O torno Leonardo da Vinci se constituía simplesmente de um pedal e da roda que mantinha o movimento inercial.
Mais tarde, pela necessidade de uma velocidade contínua de rotação, foi criado o Torno de Fuso. Esses tornos necessitavam de duas pessoas – ou mais – para serem utilizados. Enquanto um servo girava a roda, o artesão utilizava suas ferramentas para dar forma ao material. Esse torno permitia que objetos maiores e com materiais mais duros fossem trabalhado.
O inglês Henry Moudslay, criou o primeiro torno a vapor. Essa invenção não só diminuía a necessidade de mão de obra, uma vez que os tornos podiam ser operados por uma pessoa apenas, como também fez com que a mão de obra se tornasse menos especializada. Outro mecanismo que criou, permitia que a ferramenta ficasse fixa durante o trabalho, aumentado a sua precisão.
À medida que a manufatura tornava-se mais mecânica e menos humana, as caras habilidades dos artesãos eram substituídas por mão de obra barata. Isso deu condições para que Joseph Whitworth, em meados do século XIX, mantivesse uma fábrica com 700 funcionários e 600 máquinas-ferramenta. Moudslay e Whitworth ainda foram responsáveis por várias outras mudanças nos tornos da época, como o suporte para ferramenta e o avanço transversal.
Depois das modificações feitas por Moudsley e Whitworth, em 1906 os tornos estavam equipados com a correia motriz, movimentada por um conjunto de polias de diferentes diâmetros, o que possibilitava uma variada gama de velocidades de rotação. Sua propulsão era obtida através de um eixo acionado por um motor, o que fixava a máquina a um local específico.
Ainda sofrendo diversas modificações em seu processo, em 1960 o torno automático entra em cena. Para satisfazer a exigência de grande rigidez criou-se uma estrutura completamente fechada. A máquina é equipada com um engate copiador que transmite o tipo de trabalho do gabarito através de uma agulha.
Uma das últimas grandes mudanças nos tornos veio em 1978, com o torno CNC (Comandos Numéricos Computadorizados). O uso de um painel permite que vários movimentos sejam programados e armazenados permitindo a rápida troca de programa.
SAMOT
Fundada em 1960 por Tomislav Jancar, mais conhecido como Sr. Tomas, a Samot iniciou sua oferta de serviços para atender à então recém instalada indústria automobilística no Brasil. A primeira peça que a Samot usinou foi o Prisioneiro do motor do Fusca 1200. Utilizou um Torno Automático Traub e uma laminadora de roscas.
A Samot acompanhou o crescimento e desenvolvimento do setor automotivo, em 1984 adquiriu seu primeiro torno CNC e atualmente possui um moderno e avançado parque fabril, fornecendo soluções completas em usinagem com resultados de classe mundial.
Atualmente atende a diversos segmentos, como indústrias automobilísticas, aeroespacial, bélica e autopeças, sempre com foco em qualidade no total cumprimento de requisitos e prazos de entrega. Oferece serviços de usinagem a partir de barras de alumínio, latão e aço nas mais diferentes ligas, e de blanks forjados, fundidos e micro fundidos, além de processos como tratamento superficial de anodização dura e tratamento térmico por indução. Totalmente autossuficiente em alumínio, a empresa conta com uma unidade de produção de vergalhões em diversas ligas.
A Samot oferece uma estrutura completa de produção, do desenvolvimento de matéria-prima até a entrega do produto final, respaldada por uma equipe de profissionais especializados e equipamentos de alta performance.
Os principais processos produtivos da Samot são: torneamento, fresamento, retificação, fresamento de engrenagens, brochamento, furação, laminação, tratamento térmico por indução, rebarbação eletrolítica e anodização dura.
Principais equipamentos: torno multifuso CNC e mecânicos, tornos CNC simples e duplo, tornos de cabeçote móvel CNC, centros de usinagem, retíficas, centros de furação, rebarbadoras eletrolíticas, brochadeiras, laminadoras, têmpera por indução e linha de anodização.
As peças reproduzidas pela Samot são utilizadas em sistemas de freio, motor, amortecedor, direção, ar condicionado, injeção eletrônica – diesel/gás e gasolina/álcool – entre outros.